Key benefits
- Fully automated, uMp-TSC pipette cleaning requires only one click
- The range is around 70 kPa, and the resolution is 7 Pa.
- Closed-loop control with high accuracy and absolute accuracy of ±140 Pa
- Strong performance with built-in temperature adjustment and calibration capabilities
- Quick switching between regulated pressure and user/ATM pressure
- Compact models include a 1-channel desktop and a 4- or 8-channel 1U rack.
- DAQ device IO interface with simple add-on installation
- Short latency PC connection, open-source SDK, and automation enabled
Increase the throughput of patch-clamp recordings!
The automated pipette cleaning method created by Drs. Ilya Kolb, Craig Forest, and others has been commercialized by Sensapex, which also produces products with an exclusive license from GTRC, USA. We are honored to assist in the adoption of this straightforward but effective new invention, which operates dependably in practice and makes it possible to automate micropipette processes!
- Pipettes are typically changed after each recording and/or attempt since a perfect pipette tip is necessary to form the giga seal.
- Automated pipette cleaning allows for instant re-use, which reduces downtime and prevents additional recordings from being lost due to vibrations caused by manual handling in multi-patch investigations.
- Thoroughly verified to be safe to cells in the initial publication by the inventors (1). See also a recent article by Dr. Peng et al from Dr. Geiger's team (2), which exhibits a large increase in throughput in the multi-patch tests.
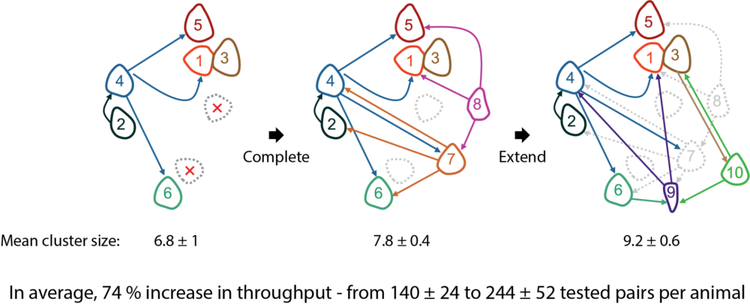
Pipette cleaning technique
The 1-click capability offered by the uMp-TSC touch screen device can be used to complete the following steps of the automated pipette cleaning procedure, which takes less than a minute:
- The pipette tip is moved by the uMp micromanipulator to a special cleaning well of the uMc pipette cleaning insert, which is filled with Tergazyme or Alconox.
- In order to bring cleaning solution to the pipette's tip, the uMc automatic pressure controller applies negative pressure to the pipette.
- To flush the cleaning solution via the tip, pressure is automatically varied between the positive and negative values.
- To completely remove all cleaning solution from the pipette with a 10x safety factor, a positive pressure pulse with a prolonged duration is used.
- For added safety, the pipette tip is transferred to the designated rinse well of the cleaning insert.
- To cycle the washing solution through the tip, pressure is automatically varied between the positive and negative values.
- The pipette tip is precisely repositioned in its initial position.
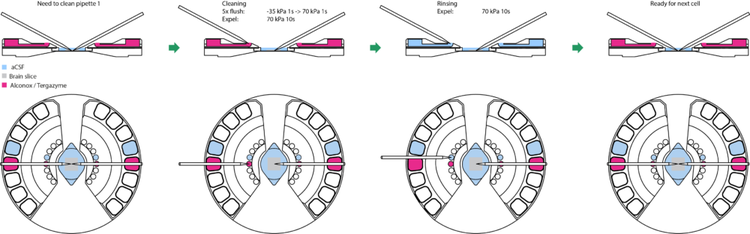
Automated control of patch clamp pressure
The optimum data production and quality for patch clamp recordings can be obtained by optimizing and consistently applying pressure settings with uMc automated pressure controllers. To configure and adjust the desired values for each step of the whole-cell patch clamp recordings in vitro and in vivo, 1-click quick buttons are accessible at the uMp-TSC. For completely automated patch clamp procedures, please refer to uM workstations.

uMc products overview
- The uMp-TSC touch screen unit offers an easy-to-use standalone user interface for operating and configuring uMc-PPC automated pressure controllers. This interface includes quick buttons for saving and establishing specified pressure levels as well as 1-click automated pipette cleaning.
- The 1-channel desktop version with an optional DAQ interface, as well as the 4 and 8 channel rack-mounted product variants, are all part of the uMc automated pressure controller product line.
- The uMc-LQS accessory uses optical sensing to detect potential fluid in the pressure tube and stop it from getting into the uMc-PPC products.
- To meet the criteria for the uMc-PPC input pressure, uMc-PRF products incorporate high quality pre-regulation and filtration of the pressure supply. There is a VAC variant that offers vacuum generation.
- Warner PM platform is suited for standard uMc pipette cleaning inserts. It is positioned on the left or right side(s) of the chamber and has four pipettes' own specialized cleaning and rinsing wells (8 pipettes when placed on both sides). During the course of the experiment, reservoirs passively maintain a constant solution level at the cleaning and rinsing wells.
Configuration examples
Automated 1-channel pipette cleaning
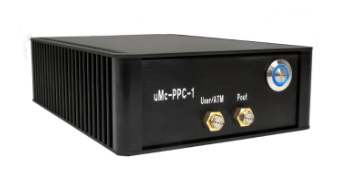
uMc-PPC1 1-channel pressure controller
uMc-PRF Pressure pre-regulation & filter unit
uMc-SLC Cleaning insert for Warner PM platform
Quad multi-patch with automated pipette cleaning
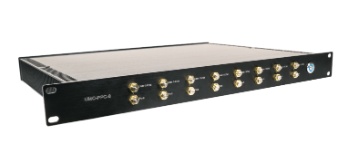
uMc-PPC4 4-channel pressure controller
uMc-PRF-VAC Pressure pre-regulation & filter unit with vacuum generation
uMc-SLC Cleaning insert for Warner PM platform
Automated multi-patch with eight channels

uMc-PPC8 8-channel pressure controller
uMc-PRF-VAC pressure pre-regulation & filter unit with vacuum generation
uMc-LQS8 8-channel liquid sensor
2 pcs of uMc-SLC Cleaning insert for Warner PM platform
uMc-PPC1 Pressure controller
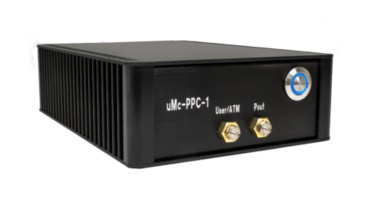
Output pressure +70 kPa
Output vacuum -70 kPa
Resolution 7 Pa
Accuracy ±140 Pa
Input pressure required +80 kPa
Input vacuum required -80 kPa
Analog I/O Control Optional
Dimensions 128 x 204 x 52 mm
uMc-PPC4/8 Pressure controller
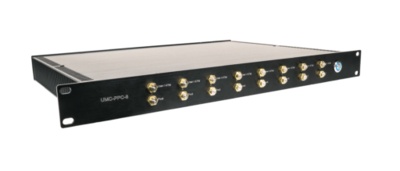
Output pressure +70 kPa
Output vacuum -70 kPa
Resolution 7 Pa
Accuracy ±140 Pa
Input pressure required +80 kPa
Input vacuum required -80 kPa
Analog I/O Control Included
Dimensions 483 x 357 x 44 mm
uMc-SLQ Optical safety switch
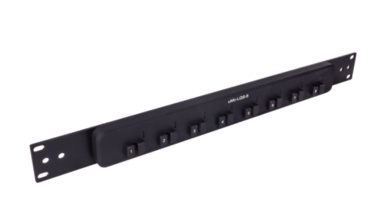
Max channels 8
Dimensions 483 x 60 x 44 mm
uMc-PRF Pressure pre-regulator & filter unit
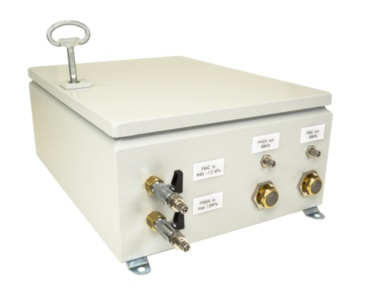
Input pressure required +150 kPa
Input vacuum required - 80 kPa
Output pressure +70 kPa
Output vacuum -70 kPa
Dimensions 304 x 467 x 163 mm
uMc-PRF Pressure pre-regulator & filter unit with vacuum generator
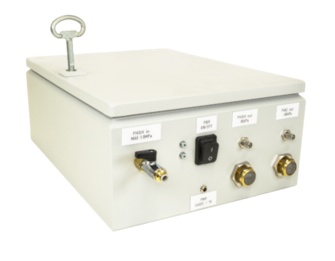
Input pressure required +400 kPa
Input vacuum required n/a
Output pressure +70 kPa
Output vacuum -70 kPa
Dimensions 304 x 467 x 163 mm
The instrument was used in these investigations:
- Cleaning patch-clamp pipettes for immediate reuse.
Kolb I et. al.
Sci Rep. 2016 Oct 11;6:35001 - High-throughput microcircuit analysis of individual human brains through next-generation multineuron patch-clamp.
Peng Y et al.
Elife. 2019 Nov 19;8. pii: e48178.